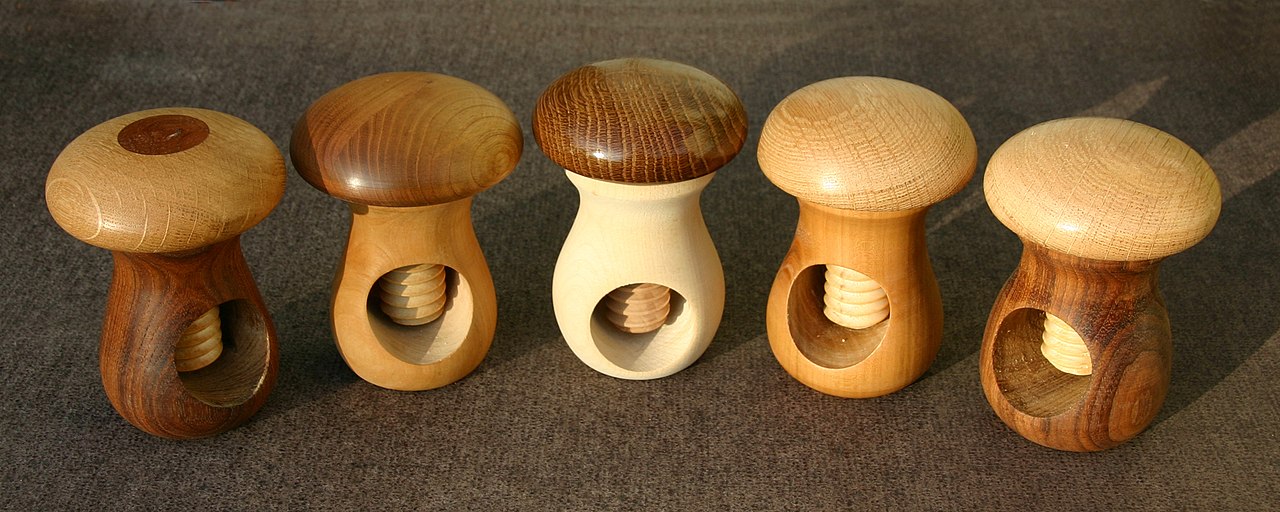
Philip Moulthrop started turning wood in 1979 after learning from his father Ed Moulthrop. Using a hand-forged lathe and chain saw, he roughs out the green sections of trees from southeastern regions. He then finishes the bowl with several coats and refines it on his lathe. The entire process takes between four and one year. Once they're done, you can either buy the bowls or give them as gifts.
Philip Moulthrop
Phillip Moulthrop is known for his bowl made of red leopard maple. Three generations have been carrying on the family tradition of wood turning. Philip Moulthrop has made bowls for several notable museums and private collections. Here are some their most iconic pieces. Continue reading for more information about this gifted artist.
Philip Moulthrop, an American painter, was born in 1947. He studied general arts in his early 20s and developed an early passion for woodworking. He bought his first lathe at age 16 and slowly expanded his equipment. He was an innovator in his field, creating beautiful turned vessels that were well-received by the art community and the United States president. After his work was acknowledged, he began to sell his pieces at local craft fairs. His work began to be recognized internationally.
Matt Moulthrop
The Matt Moulthrop Boulbows are a fine example of Georgia’s rich wood-turning heritage. The artist was born in Atlanta. He earned his BA and MBA at Georgia Tech. While he did spend a few years in the 9-to-5 industry, he never lost passion for turning wood. His bowls were recognized throughout the country. His works can be seen at the ASU Art Museum and Carter Center, as well as the Racine Art Museum.
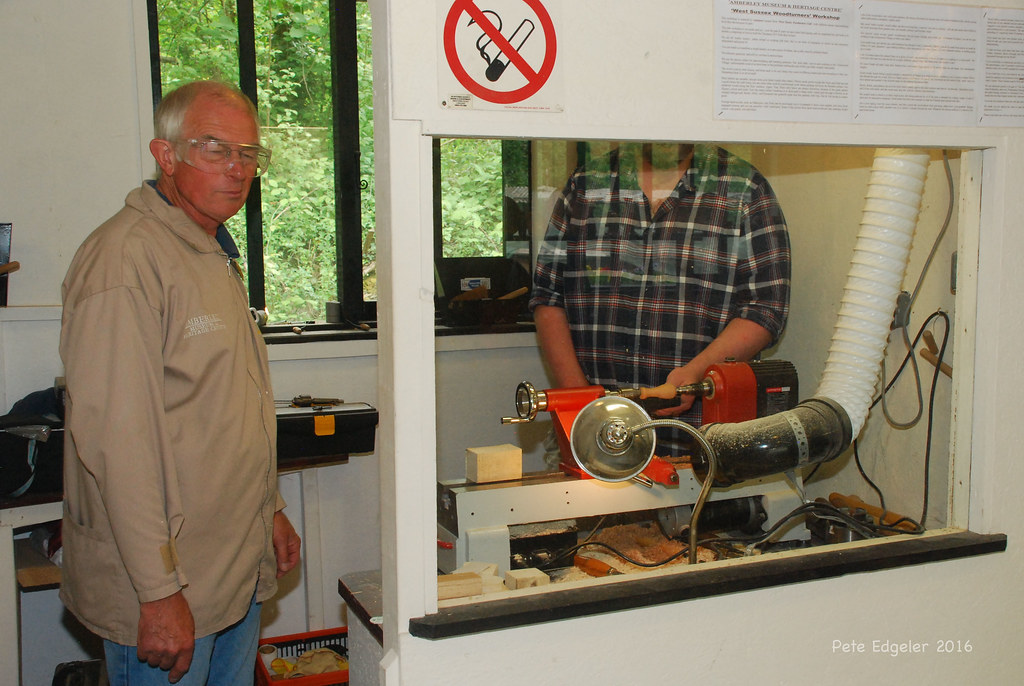
The Moulthrops have been recognized as world-class wood-turners, with works placed in prominent collections in the United States and abroad. Moulthrops' pieces are on display at the Renwick Gallery of the National Museum of American Art. Collectors from all over the globe have taken to heart his bowls. He signed each photographer's copy of the family book during a Smithsonian photo shoot.
Ed Moulthrop
Moulthrop began to turn bowls around 1970s. Soon after, he received a scholarship at Princeton University to study architectural design. Moulthrop decided to take up woodturning after spending a whole year in Vietnam. His large-scale, turned bowls are internationally recognized and can be found in museums like the Museum of Arts and Design in New York and the White House Collection of American Crafts. These bowls are made from domestic woods and polished to a transparent finish.
The Ed Moulthrop rare bowl measures nine by fourteen inches in size and is made from wild cherries. These wood bowls are available at Gump's San Francisco. There are many other pieces of Ed Moulthrop's wooden bowls on display. The best way for you to learn more about this artisan is by visiting the exhibition. He also creates a gorgeous catalog of his work. While it is possible to purchase the bowls from museums, it's best to visit his studio and see it in person.
The Eagle & Phenix Dam Series
This limited edition series is made with wood from the Eagle & Phenix Dam. The bowls retain traces from history and are made by Philip Moulthrop (local artists). They are available to bid during regular museum hours. Additionally, a portion will be offered for sale live.
The Moulthrop family has contributed to the growth of wood-turned bowls in Georgia. The museum proudly displays works by all three generations of the Moulthrop family, who have been turning bowls for more than five decades. Many of these pieces are extremely prized because they have large sizes and smooth polished surfaces. His mosaic bowl technique, which involves glueing thin branches to a shaped bowl with thin branches, is featured in the exhibit.
Matt Moulthrop's works
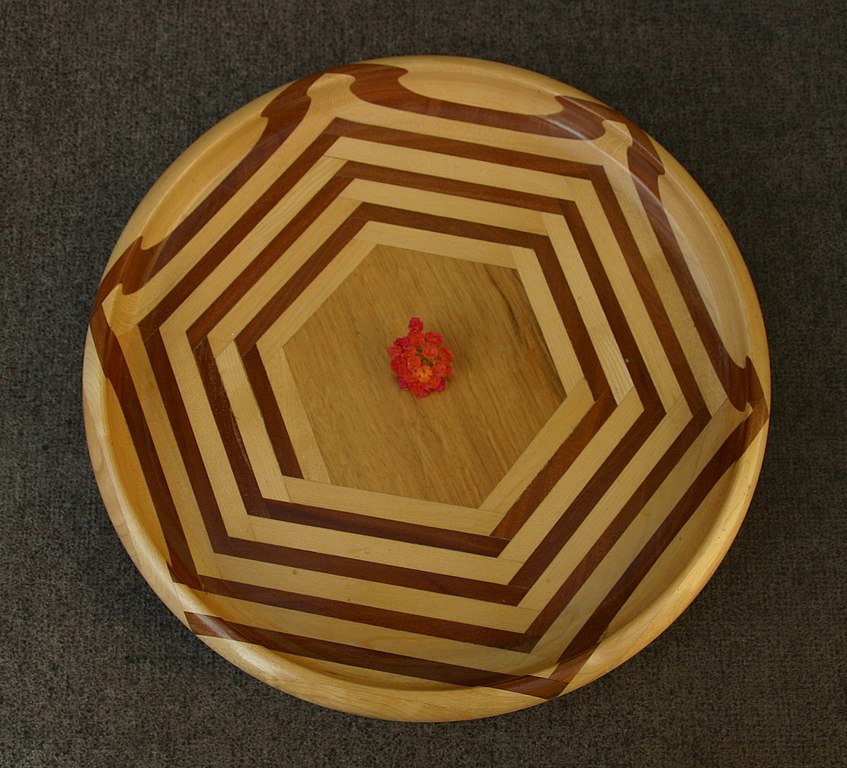
A son of Philip and Ed Moulthrop, Matt Moulthrop grew up around woodturning. From a young age, his father taught him woodturning and he has never stopped loving it. Matt started his woodworking career after completing his BA degree at the University of Georgia. He also completed his MBA at Georgia Tech. He is now the third generation who makes wooden vessels. His work can be found in many prominent institutions, including the ASU Art Museum or the Carter Center. He is currently working to create commemorative pieces for Georgia Tech Alumni Association's 100th Anniversary.
Georgia is not the only place he can turn wood. To find wood that is not common, he travels around the world. He transforms trees from around world using tools and an hand-forged lathe. This creates unique pieces. His pieces include wood harvested from trees that have fallen in the Southeast as also exotic locations such as volcanoes, underwater forests, and other places. Check out his work if you enjoy it!
FAQ
How much money do you need to get going?
Since every project differs, it is impossible to give exact numbers. These factors will help you get an estimate of how much money is needed.
-
Material costs
-
Tools and equipment
-
Time spent on the Project
-
The hourly rate
-
What is your expectation for profit?
-
It doesn't matter if your goal is to hire help
It's a good idea for beginners to start with small projects like frames and boxes. As you gain experience, more difficult projects will become possible.
What kind of tools are used to carpenters?
A hammer is the most commonly used tool by carpenters. A hammer is used for pounding nails into wood. A hammer is used to hold pieces together during a project. Other tools include clamps. pliers. screwdrivers. measuring tape. pencils. saws. drills. wrenches.
Where can I purchase woodworking supplies
There are plenty of places where you can find everything you need to start out. For example, you could visit local hardware stores or look online at websites like Amazon.com.
You can also search flea and garage sales for furniture and other materials that can be reused.
How much should a Woodworker Charge per Hour?
The hourly rate paid to a professional woodworker is dependent on many factors. These include skill level, availability, and location.
An hourly wage for skilled woodworkers is between $20 and $50.
A less experienced woodworker may charge as little as $10 an hour.
How can I learn basic woodworking skills
A great way to start learning how to build furniture is by building a simple bench for yourself. This project can be completed with whatever wood you have available at home. If you're not sure which kind of wood to choose, you can purchase cheap pine boards at Lowes and Home Depot. After you've constructed your bench you'll want sand all the rough edges off and varnish it.
Can I refinish my own furniture?
Yes! Yes! There are many methods to refinish antique furniture without hiring a professional. Here are some examples:
Use sandpaper for removing stains and scratches. Next, wipe the surface clean with a damp cloth.
Apply clear polyurethane varnish. Let dry completely before moving furniture around.
Paint furniture with acrylic paint.
Stain can be used instead of paint. Furniture will look richer with the stain.
Apply shellac wax. You can protect your wood with wax and give it shine.
Statistics
- Overall employment of woodworkers is projected to grow 8 percent from 2020 to 2030, about as fast as the average for all occupations. (bls.gov)
- In 2014, there were just over 237,000 jobs for all woodworkers, with other wood product manufacturing employing 23 percent; wood kitchen cabinets and countertop manufacturing employing 21 percent. (theartcareerproject.com)
- The best-paid 10 percent make $76,000, while the lowest-paid 10 percent make $34,000. (zippia.com)
- If your lumber isn't as dry as you would like when you purchase it (over 22% in Glen Huey's opinion…probably over 10-15% in my opinion), then it's a good idea to let it acclimate to your workshop for a couple of weeks. (woodandshop.com)
External Links
How To
How to join wood with no nails
Woodworking is a favorite hobby. It's fun and relaxing because you can use your hands to make something useful from wood. However, there are times when you want to join two pieces of wood together without having to use nails. This article will explain how to do this so that your woodwork projects stay beautiful.
Before you can join the wood pieces together, you need to remove any rough edges. Avoid leaving sharp edges that could lead to problems later. Once you've done this, you're ready to start gluing your boards together.
When working with hardwood, glue should be applied only to one side. Use glue on both the sides for softwoods, such as cedar or pine. After applying the glue, press the boards firmly until they are completely stuck together. Before you proceed to the next step, be sure to let the glue dry completely.
After you glue your boards together, drill holes at the joints where screws will be inserted. You can choose the type of screw to determine the size of your holes. If you plan to use a 1/2 inch wood screw, drill a hole at least 3/4 inches in depth.
After drilling your holes, drive the screws into the board's backside. Do not hit the boards' front surfaces. It will ruin the finish. When driving the screws, try to avoid hitting the ends of the screws too much. This will avoid splitting in the wood's ends grain.
You'll need to protect your completed project from the elements. You can either seal the entire piece of furniture or cover the top. You'll want a product that lasts for many years. Oil-based varnishes are, among others, polyurethanes shellac, laquer, and other oil-based products.
These products can generally be found in any home improvement shop. It is important to ensure that you purchase the correct product for the job. Keep in mind that certain finishes can be toxic and should not be used indoors. When handling certain finishes, wear protective gear.