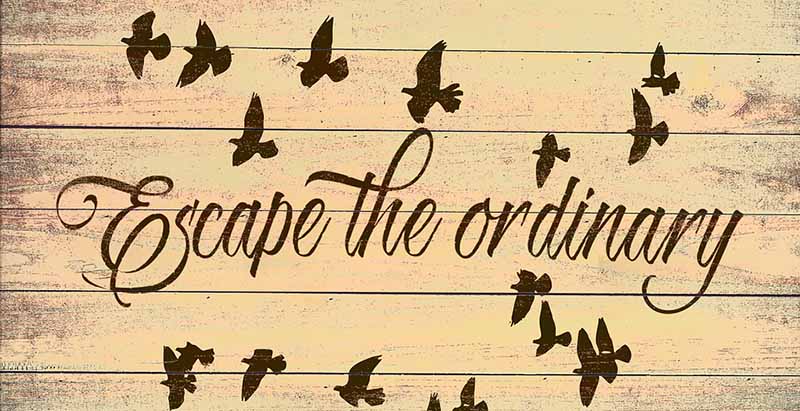
There are many materials available to make wood burning art. Basswood is an excellent choice if you are looking for a transparent color with no grainy flecks. This type of wood can however be very costly and difficult for you to find in your desired size. Birch wood is another popular choice. It has a beautiful texture and bright color. There is no variation in the color of the annual rings.
Preparing wood and other materials for pyrography
Preparing the wood that you will use is the first step of pyrography. Dark wood does not show the art very well, and a pronounced grain pattern will make the art hard to work with. Resinous woods and uneven timber are also bad choices for pyrography. It is important to use natural wood and sand it until it has a smooth surface. You can now start burning the wood once you have prepared it.
Shellac is an option to seal pyrography project, but this is only temporary. Shellac causes wood to discolor when it is exposed to heat and should not therefore be used on cutting boards nor coasters. Paste wax, which is cheaper than shellac, can be used in place of it. Paste wax gives wood a smooth, natural sheen when it is applied. It is easy to apply, and it looks natural.
Adding design to wood
You can add design to wood burning art by sketching out a rough outline of the design you would like. This can be done with a pencil or eraser, ruler, ruler, compass, or printed templates. Premade stencils can be very useful. A wood burning set includes all of the tools necessary for beginners. Below are some wood burning design suggestions to get you started.
You can also paint on the burned art. You can use either a pointed pen, or a flat pencil. But be careful not to burn too much or you might end up with holes. Wood burning art can also be painted. After you are done, you can add color to your wood burning art. After the wood cools, you can add shading.
Creating Lichtenberg burns

Lichtenberg burning is an art form that has great potential. Branching electrical discharges can be created by using a microwave converter and a high-voltage source. Lichtenberg first discovered Lichtenberg figures in 1777. Lichtenberg's wood burning is becoming a more popular form of art thanks to fractal wood burning. These are the steps to creating these figures.
Safety equipment is required before you can begin. Commonly, high-voltage transformers are used to power neon signs and appliances. These transformers can be exposed to live electricity wiring and are therefore more susceptible to electrocution than low voltage electricity. Also, you should wear gloves when operating a Lichtenberg device. Rubber gloves are also recommended. Wearing gloves is a good idea. Only touch one hand at the time and hold the other behind your back. Even though you might be electrocuted even if your hand touches an energized electrode for a while, it won’t cause your heart to stop beating. You should always bring someone with you when using a Lichtenberg tool. This second person will be there to turn off the electricity if you get electro
First, you will need a power supply. A high voltage electrical source is necessary to operate a Lichtenberg apparatus. To burn wood safely, the electrical current must not exceed 2,000 volts. The majority of woodworking associations forbid the use this technique. Safety is paramount, no matter how you create a Lichtenberg-like figure. Use gloves and protective clothing whenever you work with electric current. Double-check your electrical outlet before contacting.
Using a stencil
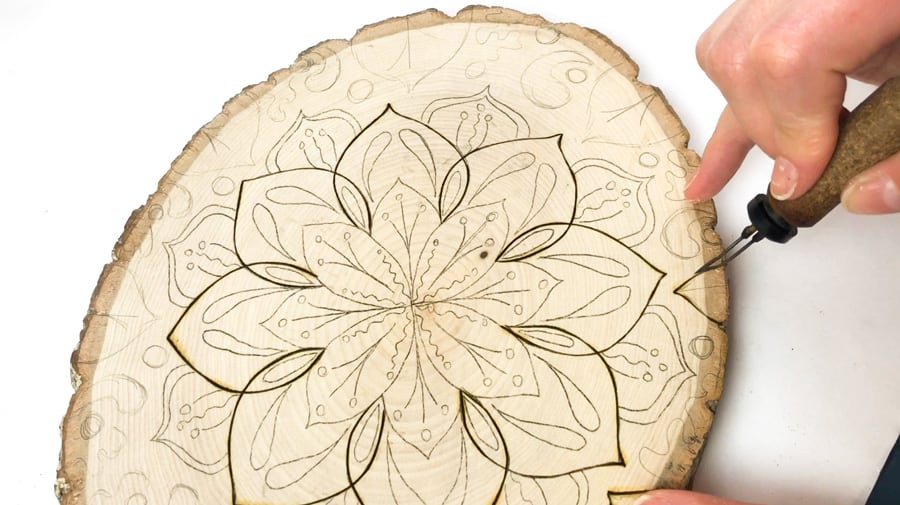
A stencil is a great tool for creating intricate wood-burning designs. You can trace a design on a graphite sheet, and then transfer it onto the wood. Although the stencil will be a guide for your eyes and hands, you can create your own design. While it is possible to use a pencil to draw a pattern, holding the stencil and the wood at the same time can result in burns.
First, you have to sand down the wood that will be used for the image. Once you've sanded the wood, you can begin working on the design. To make sure your design is as clear as you can, you will need to apply some pressure. This will transfer the graphite on the wood. Once you are done, remove the tracing papers.
FAQ
How long does it take you to finish a piece?
It all depends on how large the furniture is. You can finish smaller projects, such as boxes or picture frames, in one day. Larger projects such as tables and desks can take several days to complete. It takes time for the wood to be stained and sealed properly.
Where can I begin with woodworking
It is best to actually build furniture to learn how to make it. You'll need tools, and you'll have to make mistakes along the way, but if you keep at it, you'll eventually figure out what you're doing.
Begin by choosing the project that you want to finish. It can be as simple as a small box, or as complex as a complete entertainment center. After you have decided on a project to work on, contact a local woodworker that specializes in this type of work. Ask them for their advice about the tools and where they can be found. You might even ask whether there's someone else you can talk to who does this kind of work.
What kinds of woods are good for making furniture?
Woods are classified according their hardness. Softwoods include cedar and pine as well as cedar and cedar. Because they are resistant to rot, softwoods are often used as outdoor furniture. These hardwoods include maple, mahogany and teak. They're generally used indoors because they won't weather well outdoors.
How often should I buy new supplies?
You may have to replace certain tools. If you're using hand tools, you'll need to sharpen them regularly. If you are using power tools, you will need to purchase replacement parts regularly. Try spreading your purchases over a few months so you don't buy too many at once.
How do you know which type of wood you are working with?
When purchasing wood, always check the label. The label should include information about the wood species and its moisture content as well as whether or not it has been treated using preservatives.
Statistics
- If your lumber isn't as dry as you would like when you purchase it (over 22% in Glen Huey's opinion…probably over 10-15% in my opinion), then it's a good idea to let it acclimate to your workshop for a couple of weeks. (woodandshop.com)
- The U.S. Bureau of Labor Statistics (BLS) estimates that the number of jobs for woodworkers will decline by 4% between 2019 and 2029. (indeed.com)
- Average lumber prices rose about 600 percent between April 2020 and May 2021. (familyhandyman.com)
- The best-paid 10 percent make $76,000, while the lowest-paid 10 percent make $34,000. (zippia.com)
External Links
How To
How to join two pieces of wood together without nails
Many people love woodworking. Woodworking is a relaxing hobby that allows you to use your hands to create useful things from wood. However, there are times when you want to join two pieces of wood together without having to use nails. This article will show you how to do it to make your woodwork projects look great.
First, remove any sharp edges from the wood pieces before you join them. Do not leave any sharp corners as they could cause problems down in the future. Now it's time to start glueing your boards together.
When working with hardwood, glue should be applied only to one side. You should glue both sides if you are working with softwoods such as pine and cedar. Press the boards down until the glue is fully incorporated. Be sure to let the glue dry before you move on to the next step.
Once you've glued your boards together you will need to drill holes in the joints to accommodate screws. The size of these holes depends on what type of screw you choose to use. For example, if your screw is a 1/2-inch wooden screw, drill a hole that is at minimum 3/4 inches deep.
After drilling the holes, you can drive the screws into your board's backside. You should be careful not to touch the board's front surface. This could cause damage. Be careful not to drive the screws too hard at the ends. This will help prevent splitting of the end grain.
Once your project is complete, it's time to protect it against the elements. You can either cover the entire furniture or just the top. It doesn't matter what method you use, you want something that will last many years. There are many options: oil-based varnishes; polyurethane; shellac; lacquer.
These products can generally be found in any home improvement shop. You should make sure you are getting the right type for the job. Keep in mind that certain finishes can be toxic and should not be used indoors. Protective gear should always be worn when handling these finishes.